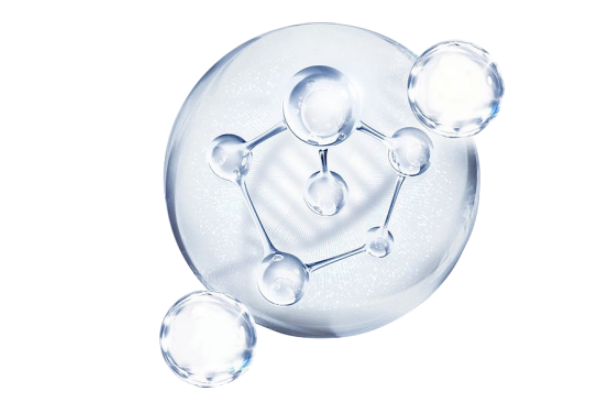
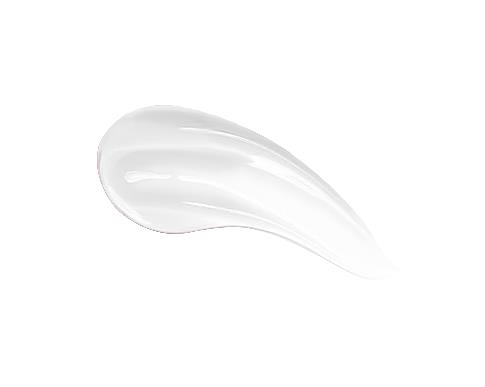
Introduction and working principle of paper chemicals
Chemicals commonly used in paper machines: flocculant, calcium carbonate, pulp starch, pulp sizing agent AKD, pulp sizing agent ASA, dry strength agent, dye, retention aid, defoamer, pulp whitening Agent, drying cylinder stripping agent, cleaning agent, cleaning agent for net part, cleaning agent for pressure part, bactericide, caustic soda, citric acid, alkaline cleaning aid, surface glue starch, surface glue amylase, surface sizing agent, industrial liquid Aluminum sulfate, etc.
Flocculants
Function of flocculant: flocculate suspended solids in white water, reduce white water turbidity and improve water quality.
Adding point: White water clarifier Adding amount: 5-10PPMCalcium carbonate
Calcium carbonate function: Calcium carbonate is filled in the fiber voids to make the paper even, improve the whiteness and opacity of the paper, and replace the fiber to save costs.
Disadvantages: It will lead to lower paper strength and affect the paper index.
Adding point: the outlet of the paper machine mixed pulp pump of the paper machine flow delivery system or the inlet of the white water tank outside the machine.Intrastarch
There are currently two types of starch in pulp, cationic starch and amphoteric starch, which need to be gelatinized before use. The main function is to improve the indicators of paper breaking resistance, folding resistance, and interlayer bonding force.
The action principle of starch in the pulp: the negatively charged fibers are adsorbed on the cationic groups of the starch in the pulp, so that the fibers are combined to increase the dry strength and improve the physical strength (burst resistance, surface strength, etc.) and retention rate of the paper .Internal sizing agent
There are two main types of internal sizing agents, AKD and ASA, whose main function is to adjust the water absorption value of paper.
The mechanism of action of AKD (alkyl ketene dimer): under medium-alkaline conditions, the AKD reactive functional group can react with the hydroxyl group on the cellulose to form a covalent bond and fix it on the fiber, forming a A stable film layer changes the fibers from hydrophilic to hydrophobic, thus making the paper sheet water resistant. Influencing factors are: system PH value, drying temperature, paper moisture, etc.
The principle of ASA action: the acid anhydride in the ASA molecule has high reactivity, and can react with the hydroxyl groups of cellulose and hemicellulose to form ester bonds, so that the ASA molecules are oriented, and the hydrophobic long-chain olefin groups point to the outside of the paper, so that Gives water resistance to paper.
The main difference between ASA and AKD: ASA sizing cures quickly, and the curling lower roll can cure AKD needs a certain reaction time to fully mature.
Adding point of ASA and AKD: Paper machine flow delivery system pressure screen feeding pulp pump outlet pipe.Dry strength agent
The main function of dry strength agent is to enhance the hydrogen bonding force between fibers, and improve the ring compressive strength, tensile strength, bursting strength and interlayer bonding force of paper.
The working principle of dry strength agent: most of the natural and synthetic dry strength agents are hydrophilic polymers, and these polymers are dispersed among the fibers to increase the number of bonds between fibers, thereby achieving the purpose of improving the strength of the paper. Most dry strength agents contain cationic groups connected to the main chain ring, which increases the binding force between the polymer and the fiber and improves the retention of the polymer. Commonly used dry strength agents include natural polymers such as starch and its modified products (such as cationic starch, anionic starch), synthetic polymers such as polyacrylamide, glyoxal polyacrylamide and polyvinyl alcohol, and other water-soluble natural products. Kind of dry strength agent. In most cases, the effective dry strength effect can be achieved only by adding 0.1%~0.35% of such substances by mass fraction. In my country, anionic polyacrylamide and modified starch are the main products.
From the characteristics of their molecular structure, dry strength agents are mostly polymers containing polyhydroxyl groups, which is the basis for forming hydrogen bonds with cellulose molecules. The hydrogen bond forming groups in the dry strength agent molecules and the fiber surface The hydroxyl groups form hydrogen bonds. For example, the free glucose hydroxyl groups of starch participate in the formation of hydrogen bonds of cellulose molecules on the fiber surface, so starch increases the binding force of internal fibers and increases the number of hydrogen bonds on the natural bonding surface between two bundles of fibers. At the same time, the dry strength agent has a certain improvement effect on the paper sheet forming process. The dry strength agent acts as a high-efficiency dispersant at this time, that is, the dry strength agent makes the fiber distribution in the pulp more uniform, and provides more inter-fiber and fiber-high Intermolecular bonding, thereby increasing dry strength.
Adding point of dry strength agent: inlet pipe of paper machine mixing pulp pump.Dye
There are three kinds of dyes commonly used in the production of cultural paper and white cardboard: purple dye, blue dye and whitening agent.
There are four kinds of dyes commonly used in the production of kraft cardboard: black dye, red dye, yellow dye and brown dye.
The dye addition point is the inlet of the slurry feed pump of the flow-through slag cleaner.Retention and drainage aids
Paper retention and drainage aid is a water-soluble branched organic polymer.
The role of the papermaking retention and drainage aid is to increase the retention rate of the pulp when it is online, and it has an excellent retention effect on fine fibers and fillers (calcium carbonate, titanium dioxide and kaolin, etc.), and the pulp is obvious. Enhance drainage, reduce dehydration energy consumption during forming, pressing and drying. Thereby increasing paper production, reducing energy consumption and reducing costs. It also has the effect of increasing the strength of wet paper and dry paper, keeping the chemical conditions of the wet end stable, improving the paper formation and paper physical properties. Due to the reduction of fine fibers and fillers in the effluent, the load of wastewater treatment is also reduced.
Paper retention and drainage aids are mainly polyacrylamides, and there are also starch modified products. Most polyacrylamides are imported cationic products, including powder and emulsion. Emulsion products occupy half of the country due to their good retention and drainage effects, good fluidity and fast dissolution speed.
There are two types of emulsions: water-in-oil and water-in-water. The performance of water-in-oil products is good. The only weakness is that it contains mineral oil, which costs a lot, and the oil enters the pulp to cause secondary pollution, which may also affect the quality of paper. Water-in-water emulsion products also have the advantages of water-in-oil emulsion, and because the production is dispersed polymerization in the water phase, the cost is relatively low. No pollution, does not affect the paper quality. Water-in-water products are widely used abroad. It has also begun to be gradually applied in China.
Filter aids are chemicals added to improve the drainage and dehydration speed of wet paper from the papermaking wire section. The filter aid can mainly make fine fibers flocculate on the surface of the fiber, which can reduce the clogging of wet paper pores and increase the permeability. Drainage and retention are interrelated in promoting dispersed flocculation. So there are many similarities between the two in terms of performance. The types of filter aids mainly include polyethyleneimine, polyacrylamide, polyaminoamide, cationic ethylene series polymers, etc. The initial filter aid used was polyethyleneimine. Later, due to the price reduction of polyacrylamide and the development of various modified polyacrylamides, the application of PAM gradually became the mainstay.
The addition point of retention aid and filter aid is generally at the outlet of the pressure screen in the flow delivery section.Defoamer
The principle of action of the defoamer: by reducing the surface tension of the foam, it destroys the elasticity of the foam film and causes the foam to burst.
There are three main types of foam: one is the foam floating on the liquid surface; the other is the air dissolved in the slurry; the third is the fine foam adsorbed on the surface of the fiber and inside the fiber.
Hazards of foam: The high content of air bubbles in the slurry not only affects the dehydration of the wire part, causes paper defects, reduces the machine speed, and causes paper breaks, but also easily reduces the operating efficiency of the pump, increases energy consumption, and makes the entire flow delivery system unstable. Even cause the tripping and shutdown of the sizing pump. According to research, air bubbles with a diameter less than 0.8mm often cause bubbles in the wet paper formed by the wire part and poor paper uniformity, which hinders the combination of fibers and fibers, and the cardboard is easy to delaminate, and in severe cases, full-width delamination occurs. General research and production experience show that when the air content in the slurry exceeds 0.5-0.6%, it will have a greater impact on the quality of the paper.
There are several types of paper defoamers:
One is kerosene, the other is oil and ester, the third is fatty alcohol, the fourth is polyether, and the fifth is silicone.
The kerosene-based defoamer can only eliminate foam on the water surface, and has poor ability to remove gas from the slurry, and it will also affect sizing, making the finished paper smell of kerosene, so it can only be used for low-grade paper such as corrugated paper.
Oil and ester defoamers can only eliminate surface foam, the degassing effect is poor, and also affect sizing, and the price is higher; silicone defoamers can only eliminate water surface foam, and the amount is large, economical Sex is not good.
Polyether defoamers are easily affected by temperature. When the white water temperature is different, the defoaming and degassing effects are quite different.
Domestic defoamers are mainly hydrocarbons, oils and silicones, and the most prominent advantages of fatty alcohol defoamers are that they can quickly and quickly remove the gas in the slurry and eliminate the foam on the water surface. The least impact, and the use of low cost, is the development direction of today’s papermaking defoamers.Dryer stripping agent
Cylinder stripping agent is a chemical product that solves the problems of cylinder sticking and paper powder falling in various paper production.
The working principle of drying cylinder stripping agent: form a layer of film on the surface of drying cylinder, reduce the wear of drying cylinder and scraper, solve the problem of cylinder sticking, and play the role of stripping and lubrication.
Dryer stripper chemical composition: a mixture of mineral oil and fatty acid ester
Advantages: It is self-lubricating and easy to emulsify in cold water. Excellent lubricity and stripping properties minimize wear on cylinder surfaces and scrapers to increase productivity. It has excellent peeling performance and can reduce the occurrence of paper dust.
Solubility: It is easy to disperse and emulsify in cold water under slight stirring.
Ten, wool cleaning agent, cleaning agent
The main function of wool cleaning agent is to clean the pollutants on the felt, improve the air permeability and absorbency of the felt, and improve the dehydration ability of the felt.Net cleaning agent
The main function of cleaning agent for hair part: to form a layer of cationic protective film on the surface of the forming wire and the hair part, to isolate the forming wire and stickies, to prevent the stickies from adhering to the wire surface, and to protect the forming wire.Fungicides
There are many types of fungicides for papermaking, which can be divided into inorganic fungicides and organic fungicides according to their molecular structures.